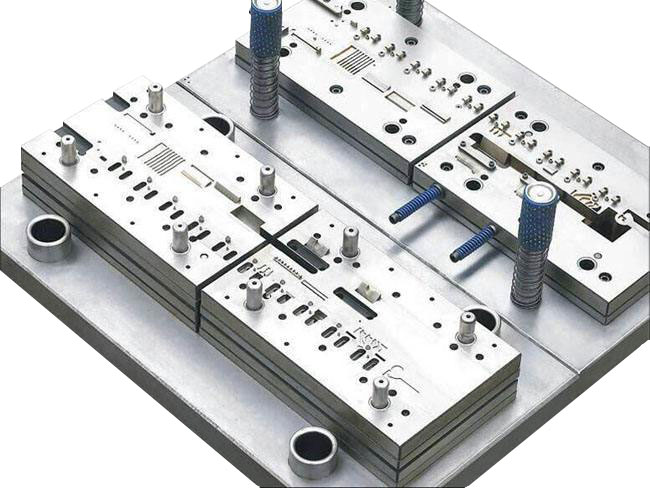
Non-standard Equipment, Non-standard Parts, and Non-standard Tooling Design
I. What is Specific About Non-standard Mechanical Design?
Non-standard mechanical design involves creating equipment, parts, and tooling that are not standardized. For example, machines like C616, C620, C630, C6125, M7475, B650, and M131 are well-known standard equipment in the machining industry. However, many specialized devices not listed as standard equipment are the focus of non-standard design professionals.
Non-standard machinery refers to mechanical products that are not mass-produced and cannot be purchased directly off the shelf; they must be custom-made by manufacturers. The same function can be achieved by machines of different sizes and configurations. Additionally, non-standard equipment is heavily influenced by the user's site conditions and other constraints.
Although the forms are not standardized, the mechanisms and parts within them do follow certain standards. Specific guidelines for non-standard equipment can be found in resources like the "Handbook of Non-standard Mechanical Equipment Design."
II. Employment Positions
Working in non-standard design is demanding and requires a strong practical foundation. Skills in turning, milling, planing, grinding, and fitting are essential. The more skills you have, the better. With this practical foundation, you can avoid being considered an outsider in machining, and you might even become a machining process engineer.
The next step is theoretical learning. You need to master specialized theoretical knowledge in non-standard design, including material mechanics, theoretical mechanics, mechanical drawing, descriptive geometry, electrical basics, computer basics, etc. Whether you pursue education before practice or vice versa, both paths are valid.
Non-standard design work covers a wide range of fields due to its nature of solving various problems. This requires designers to have extensive knowledge. The more knowledge and experience you have, the more effective you will be at solving problems quickly and accurately, thereby reducing the risk of making unusable or scrapped equipment—a common occurrence.
The prospects for non-standard design work are consistently good. Technological advancement in the world depends on this work. In companies, non-standard design is often described as the lifeblood, and in society, it is seen as the vanguard of technological progress. Therefore, this job is also honorable. Receiving an invention certificate, for instance, can be a rewarding affirmation of your contribution to technological progress.
III. Purpose of Non-standard Design
- Improve product quality.
- Increase efficiency.
- Ensure production safety.
IV. Essentials for Non-standard Design
- Necessary design handbooks, which can be downloaded online. These handbooks are invaluable resources for finding the knowledge you need. For example, if you need to design gears, the handbook will provide the necessary parameters. Always refer to the handbook first when encountering issues.
- Download catalogs of mechanical equipment to inspire your designs.
- Understand that equipment movement involves either linear or rotational motion. Mastering these mechanical principles, combined with electrical, pneumatic, and hydraulic systems, enables you to design non-standard equipment.
- Download CAD versions of standard parts and store them in your CAD design center for easy use, which will enhance efficiency.
V. Preparation for Non-standard Design
- Understand the equipment's purpose: Is it for processing, testing, or as a jig or fixture?
- Processing equipment: Ensure machining accuracy and facilitate quick and accurate loading and unloading.
- Testing equipment: Provide appropriate power, necessary testing points, and integration with electrical systems for data display and reading.
- Jigs and fixtures: Ensure reliable limitation of freedom degrees and quick, reliable loading and unloading.
- Conduct on-site investigations to gather relevant data:
- Equipment-related data such as external dimensions and corresponding drawings.
- Data on the installation site to check for interference with other equipment.
- Electrical data for the installation, including voltage and available power.
- Prepare industry standards and related data from manufacturers available online. These usually include principles, installation dimensions, etc., to aid in drawing preparation.
- Draft a feasibility report, including:
- Efficiency and accuracy of existing equipment and reasons for updates or additions.
- Features of new equipment.
- Production costs, including materials, labor, and subcontracting.
- Cost recovery period: Implement projects with an investment recovery period of less than six months; consider those with a one-year recovery period. Include savings in labor costs and increased efficiency.
- Estimated production timeline.
VI. Design Process
- Visualize the design conceptually, breaking down the equipment into major components and determining the structure and connections of each part.
- Create drawings to translate the concept into detailed plans. Start with general drawings and proceed to part drawings for easier design modifications.
- Perform strength checks. Experienced designers may select materials directly, while those with less experience should conduct simple calculations to avoid significant errors.
- Check the drawings for potential interference, installation ease, user-friendliness, and maintenance convenience.
- Organize the drawings and calculate the weight of components for quick external quotations. Pricing can be estimated by multiplying the material weight by 2-3 times the material cost.
VII. Market Research and Pricing
Inquire about the prices of designed product components and parts in the market. Use common parts as much as possible for ease of maintenance and interchangeability.
VIII. Design Advice
- New designers' work will likely be imperfect. Seek advice from experienced engineers, who generally offer guidance to improve and refine your work. Strong responsibility might cause sleepless nights, but perseverance will overcome initial challenges. Mistakes are inevitable, but learning to remedy them is crucial.
- Mechanical principles, like musical notes, are limited in number. Whether in equipment or products, it is about how you combine them. Study others' designs, understand their concepts, and apply them to your work. This is not copying but application.
- Ensure your designs are maintenance-friendly, providing easy access for tools. Consider manufacturing aspects during design, such as avoiding drilling on curved surfaces unless necessary or creating platforms for drilling.
- Optimize the initial design draft for simplicity and advanced components. For example, when designing an electric flatcar, consider the benefits and drawbacks of DC versus AC transmission, safety, and cost. Research alternatives like brushless DC motors with low RPM to avoid using a gearbox, thereby reducing investment, faults, and maintenance costs. This is innovation.