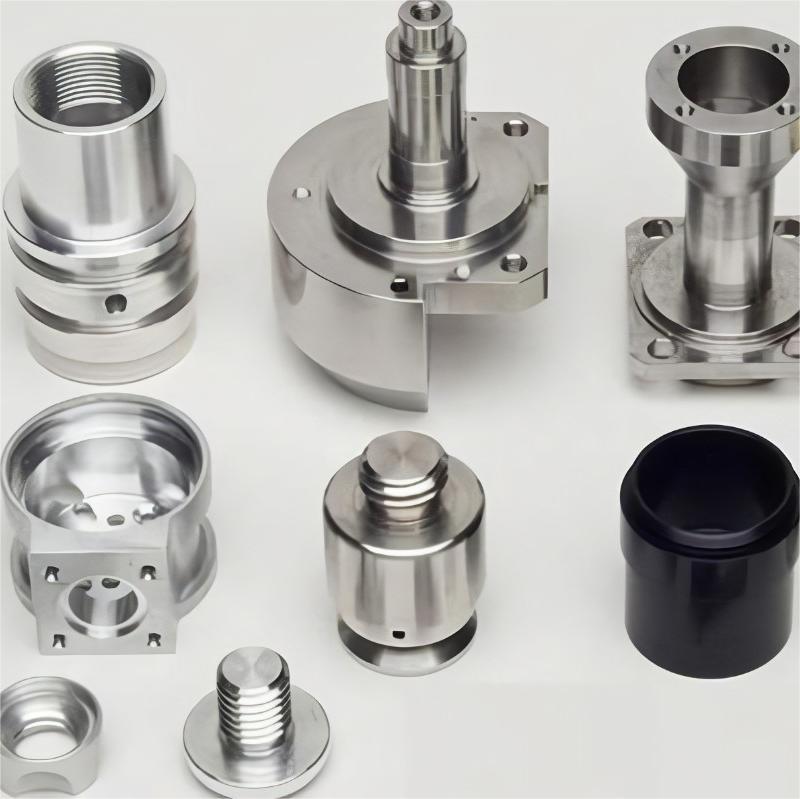
Stamping Bracket Process and Mold Design
Stamping Bracket Process: The hardware stamping bracket is a complex stamping part on a certain product, which involves multiple stamping processes such as blanking, bending, flanging, and forming. The bracket part requires a smooth surface, no burrs on the cross-section, no scratches on the surface, and dimensional tolerances of IT14 grade for mass production.
Stamping Process Solutions for the Bracket: In the mold design process, determining the stamping process is crucial as it affects product quality, production efficiency, and mold complexity. Based on the bracket part's structure, dimensions, tolerances, and technical requirements, there are several stamping forming process solutions proposed:
- Solution One: Adopt single-process stamping forming, including blanking, bending, flanging, forming, hole punching, grooving, and deburring.
- Solution Two: Adopt progressive die stamping forming, including hole punching, bending, flanging, forming, blanking, and deburring.
- Solution Three: Adopt compound die stamping forming, including hole punching, blanking, bending, flanging, forming, and deburring.
Through comparison, the first solution has low production efficiency and is not suitable for mass production of parts. The second solution involves complex mold structures, leading to relatively high production costs. The third solution offers a simpler mold structure, easy manufacturing, and ensures good quality and precision of the workpiece.
Mold Structure and Working Process:
Compound Die for Blanking: The hardware stamping bracket utilizes an inverted compound die structure. It consists mainly of rigid pusher devices, elastic unloading devices, positioning parts, punch dies, blanking dies, male and female dies, fixed plates, and pads. The mold frame adopts a smooth sliding and accurately guided column frame. The mold working process is as follows: the material strip is fed along the guide pin into the stop pin, and then the upper die descends to complete punching, bending, flanging, forming, and blanking actions. Waste from punching is ejected, and trim waste is removed using elastic unloading. The workpiece in the blanking die is ejected during the press's return stroke, completing one stamping process.
Compound Die for Bending, Flanging, and Forming: This mold mainly consists of male and female dies, elastic top piece devices, and a mold frame. The work process involves placing the blank on the female die, aligning it using two φ7 mm holes with locating pins to ensure precise positioning. The upper die applies pressure to the blank, causing bending on three sides and flanging on one side. As the upper die approaches the press's bottom dead center, it forms the bottom of the workpiece into the desired shape, creating a stable bracket part. Finally, an unloading screw pushes the workpiece out of the female die, completing one forming cycle.
Considerations:
- In the design of compound dies for blanking and forming, precise calculation of the pressure center of the stamped part is crucial to ensure alignment with the press slider's centerline. This typically involves adjusting the effective area of the blanking die to coincide with the pressure center.
- For bending, flanging, and forming processes, accurate positioning of the workpiece is essential. Utilizing pre-punched holes for alignment aids in achieving precise positioning. Additionally, controlling the die clearance during manufacture helps manage springback of the workpiece. Uneven deformation may occur during flanging, but due to the large curvature radius of the flanging line, corrective measures to the blank shape can be simplified, facilitating process calculation and mold manufacturing.